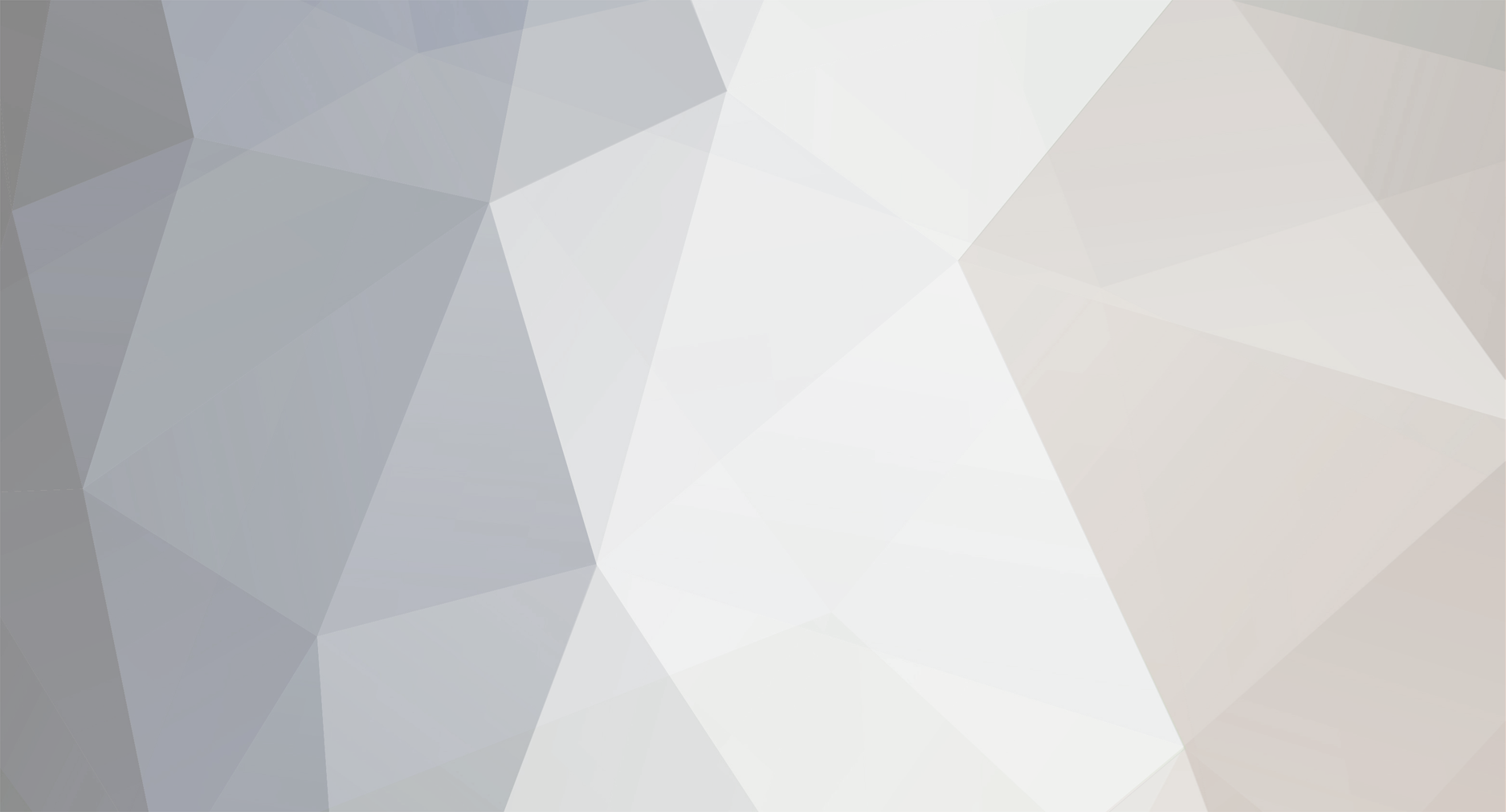
nuke
Members-
Posts
85 -
Joined
-
Last visited
-
Days Won
5
Content Type
Profiles
Forums
Gallery
Blogs
Events
Everything posted by nuke
-
As a bit of a followup, I went ahead and installed the Faber tail bushings and INSert Nashville to ABR studs into my H150. My 1998 H150 is a little bit different, as it was originally factory equipped with Tune-o-Matic tail and bridge. (heavy type and Nashville). The tailpiece bushings were not steel, but were longer than the ones in my 535. The Nashville bridge bushings were pretty much the same. Curiously, they didn't make much difference on the H150, unlike the H535. I suspect that the longer Faber bushings made far better contact with the maple center block and coupled the vibrations better to the body. I think the H150 were already well coupled, due to the solid body design of the guitar.
-
I've measured the HRW's in my 2001 H535... The magnets are almost certainly A5, but they do read a bit stronger than typical. The external appearance is the same as the Schaller pickups. I didn't unsolder the covers on mine to look inside, but they are definitely made out of Schaller components, with the different spacing of the poles for the neck and bridge, double mounting screws, etc. The rest of electrical measurements are very similar to the SD SH-2 jazz set. I'm super happy with them in the 535. I like them as much as the ThroBaks that were in a Collings I35LC I played not long ago.
-
Yeah, when I re-did my H150 pots (a 1998 that was factory SD59's) I picked values to dial in a good sound. Heritage had used the Gibson "Norlin Era" potentiometer values of 100k tone and 300k volume. That loaded it down a bit too much, and was kind of dark. The output jack was getting funky, so decided to get the pots at the same time. I experimented with the classic 500k/500k and it was a bit too brite, so went with 250k tone pots and the 500k volumes. Curiously, the same factory values used in my Heritage H535 with the HRW pickups. So Heritage was picking values in the late 90's and early 2001 era. Since the tone pots are log taper, a 250k at max is the same as a 500k dialed down to about '8' on the knob. Which for me on this guitar, was about perfect. It has the right amount of brightness opened up all the way, without getting harsh. I did 50's wiring, so rolling off the volume doesn't roll out the highs quite as much. Works pretty well on my '98 H150, as it is one of the lighter ones and very resonant.
-
Yeah, the thing is, humbuckers that follow the classic, "PAF" pattern (basically all Gibson styled humbuckers) have quite similar response curves. They're pretty flat in the lower frequency range and the differences are the resonant-peak center frequency and acuity (called "Q-factor" in electronics.) There are some things that affect them in non-obvious ways, such as the cover materials, even how they are plated. The guitarnutz2 message board has a sub-board for pickup testing and modeling, which gets quite deeply nerdy in an electrical engineering direction. I'm an EE in real life, and I have the lab equipment to measure magnetic fields, inductance, capacitance, even make Bode plots of the pickup response curves. The response curves are easily manipulated externally with simple electronics such as the guitar tone controls, or even better, an EQ pedal, like a 7 or 10 band, especially if your subtle with it. The Gibson Varitone switch is just a bunch of inductors and capacitors that are switched in order to alter the frequency response and resonant peaks of the pickups. The SD59's have a rather sharp peak in the 2.5k-2.7k range, so they're kind of bright and a bit harsh wide open. But that's ok - because rolling down the volume slightly and slightly reducing the tone knob, it shaves that peak down quite a bit. Similar effects can be achieved by using different values of tone and volume potentiometers and tone capacitors.
-
FWIW, I'm absolutely loving the HRW's in my 2001 H535 that I bought about 6 months ago. The Faber locking hardware, and surprisingly, the Faber bushing inserts for the tail and the bridge made an absolutely enormous difference in tone. I just refretted it with Dunlop 6100, as it had possibly the worst frets and fretboard I've seen on a Heritage. But those HRW's are fantastic for the blues/rock tones I like. They really complement the excellent tone of this 535. I don't mind the SD59's that came original in my 1998 H150, they're a little "harsh". Slightly rolling off the volume and tone just a little bit makes them better. My H150 is definitely one of the more resonant ones, and lighter at around 8.75lbs.
-
Thin and properly applied poly doesn't sound much different than a properly applied nitrocellulose finish. The difference in finish is far, far more apparent on acoustic guitars where the body and especially the top play an enormous role in the sound of the guitar. The idea that "poly is bad" came the era when it was applied so thickly to guitars you could chip it off with a chisel and get 1/8" flakes of it coming off. Poly has a lot of advantages, the biggest is it doesn't take much time in the factory. Once it is cured, it is stable. Not to mention the solvents and worker exposure. Rickenbacker is using a UV-cured finish currently, very little solvent is used, and it cures in minutes upon exposure to UV light. For the owner, poly doesn't shink, doesn't react with stuff, isn't easily damaged by common chemicals, like alcohol or acetone, and it is quite easy to make minor finish repairs, as it sands and polishes easily. Harder to make deeper repairs, since it is insoluble once cured. All that being said, I like nitro a lot. It feels right and I like the way it sinks into the grain over time, especially on spruce top acoustic guitars. Nitro finishes are very repairable for the experienced luthier with the proper equipment since lacquer can be blended with fresh lacquer to make nearly invisible repairs. Then we can get into the merits of hand-applied varnish finishes...
-
LOL, they do! Always thought it was weird, but kind of understand it now. I have one very nice guitar, that is so nice, that I get nervous touching it and have OCD to wipe it down every time I get it out for a while. Bought it from a friend who lives in Japan. I'm afraid to take it out anywhere. It's gorgeous and plays like a dream. But a few years ago, was offered a killer deal on a new Gibson 60th anniversary Custom Shop 1960 Les Paul reissue. It came "lightly aged". I have no "first nick" trepidation and pull it out to play with ease. I'll even take it out to a jam or what not. I've always made my own patina, but it seems to take decades. The most "patina" of mine is a 1984 Fender Esprit, and it already had some significant marks when I bought it in 1988.
-
Since I was around and 6-string aware when Heritage came along, as well as G&L, I've held both in high regard. I really fell in love with the H140 when I first set hands upon one in the 1980's. Somehow, me owning one, never happened. I can say that among my friends who knew Heritage, we tended to regard them as a "G-style" guitar that was good, more affordable and useful as a tool for the working musician who wanted a good-quality, G-style instrument that was road worthy. That seemed to be the prevailing view of the brand into the 2000's among working musicians. Used Heritage guitars from the 80's and early 90's tend have a lot of... patina in my experience. G&L's, especially ASAT's, same kind of experience. Working man's tools.
-
Nice channel on youtube. You got a lot of videos there!
-
Welcome!!! I'm almost 60 myself. Just playing devils advocate a bit, not trolling you.
-
Why not just buy a Gibson? Not trolling, but what made you get the Heritage instead of the Gibson? My first Heritage was a '98 H150 (I bought used), which was a special dealer order with Seymour Duncan 59's and tune-o-matic tail and bridge (Nashville type) instead of Schaller pups and hardware and jumbo frets. Heritage put some weird value pots in it (basically the same as Norlin era late 70's Les Pauls, 300k and 100k). I played it for almost 20 years like that. Eventually, I had to replace the output jack, so put in the excellent Dimarzio 30% taper pots at the same time (500k and 250k). Much better. Then I put Faber locking ABR bridge and locking lightweight aluminum stopbar. Then I put on a set of Gotoh SG301 locking tuners in place of the heavy Grovers. That shaved a significant weight off the guitar, 8.8lbs now, vs a bit over 9lbs. More balanced and comfortable now. The Faber stuff is great, and is more functional change than stylistic change. Locking hardware and tuners are awesome at string change. Not long ago, I bought a virtually unplayed 2001 H535. It had the typical Schaller hardware and HRW pickups. I liked the Faber stuff so much I put it on the H535, along with a set of Gotoh SG301 tuners. (the Rotomatics had gotten stiff due to lack of use). I put the Faber inserts and bushings in and holy cow, did that ever bring the tone out! I was stunned how much difference that made to the 535. I just refretted it with the same Dunlop 6100 wire too. Turns out it had some of the worst factory fretwork I've ever seen. Explains why it was unplayed so long. But now, it's a forever guitar. I love it, hands down. I've compared it with a Collings I35LC with Throbaks (excellent guitar) and I am totally happy with my 535. I even put a CNC'd nylon nut on it, because they work so much better than bone. I didn't mind the stock Schaller hardware, but I'm much more used to the conventional tune-o-matic when I play. Just more comfortable. I also own a very killer Gibson, a Custom shop 60th anniversary 1960 Les Paul v2. It is a stunner of a Les Paul as well. I know what a great Gibson should be. (where I learned the value of Nylon 6/6 nuts - which were original on all the 'bursts from the 50's and 60's) So I ask, why do you want to change your Heritages? Are you: Correcting something? Changing something for practical purposed? Changing something to suit your playing style as it evolves? Changing something for aesthetic reasons? But I would suggest if you want it to be a Gibson, find the Gibson you want and get that. There are enough, minor, but important differences, that a Heritage isn't and never will be a Gibson. My H150 is never gonna be a Gibson Les Paul, and my H535 is never gonna be a Gibson ES335, but that's OK.
-
Try this: Roll the volumes down to 9 and your tone controls down to 7. This will take the hair off the SD59's. My '98 H150 came factory equipped with SD59's. Heritage back then was equipping them with 300k volume and 150k tone pots, which smoothed them down quite a bit. A little too much in my opinion. I had occasion to replace a bad jack and a slightly scratchy pot, so I replaced the pots with Dimarzio 500k volumes and 250k tones. That's electrically, the equivalent of making 7.5 the top of the tone pots. Seems about right to me. The Dimarzio pots have a 30% audio taper, which allows smoother control of the volume as you turn down from full. The usual 10% audio taper pots are designed to give smooth control coming up from full off. I have a Gibson Custom Shop 1960 re-issue with the Custom Bucker III pickups. They're lower output, softer in the highs with a little upper high frequency shimmer. The Alnico 3 magnets are low flux, so the pickups can go closer to the strings, which they kind of need to. Had occasion to play a Collings I35-LC (ES-335 style) which was equipped with ThroBak SLE-101-plus pickups. Wow, match made in heaven. Clapton's ES335 was most likely "patent sticker" humbuckers. Lifeson's ES355 was most likely t-top humbuckers. Different tones, different eras.
-
Yeah, I had opportunity to play it for a month or two with just the bridge, then just the aluminum tail piece, then locked the tailpiece. The bushings though, made a lot of difference in sound. More so than I would have expected. I tend to think the bridge INserts were the biggest part of that. The odd ringing overtones are gone, leaves a really nice, dry, woody, mods-forward tone that I was looking for. A lot like the very expensive Collings I35-LC I played a few weeks ago. That was a nice playing and very good sounding guitar. I was a little on the fence about the bushings and inserts. Skeptical that the tail stud bushings would make any difference, and was not certain I wanted to make a change that precluded putting the original Schaller hardware back on. Once I did though, super happy with it and decided to go with the refret. I've got the frets off the H535 now, in the process of properly leveling the fretboard and re-fretting to get the playability up where it should be. I think this one left the factory with a poorly leveled fretboard, and I think a few people had a go at it over the years trying to correct the problem by leveling and crowning the frets. They still had the nibs, so it was factory frets. Someone had a ham-fisted go at it with a crowning file at some point. Also found the radius was 10" instead of 12". Not that unusual, but kind of a pointer at lax QC when this guitar was made. I think it will play super nicely. I have a CNC'd nylon 6/6 nut waiting to go on as well. (like Gibson in the 50's and 60's used).
-
A few months ago, I bought a used 2001 H535, blonde with HRW pickups. It had the typical Schaller roller bridge and top-loader tailpiece. I bought a Faber locking tail and locking bridge kit for it. Found that the tailpiece bushing holes were not deep enough to take Faber studs. Hunted around for a 11mm Forstner drill bit, eventually found one and sunk the holes another 0.21". While I had it out, the H535 bushing inserts were surprisingly short and easy to pull out. I had to raise them to get the Faber locking spacers on them to work, and it wasn't all that stable with the bushing not all the way down. So I opted to replace the tailpiece bushings with the Faber 11mm/Imperial thread, and got the INsert bridge studs while I was at it. Wow, that made a big difference. The tone greatly improved with the addition of the bushings. It really brought out that dry, woody, semi-hollow-body laminate sound. The tail studs are about 0.90" long, steel, and just slightly oversized, so they fit and bite into the wood tightly. It took some effort to press them in and flush with the to of the guitar. The real trick though are the bridge studs that replace the "Nashville/Schaller" threaded inserts. The Faber ones are much longer and have much deeper wood contact. On the 535, they couple not just to the upper laminate shell, they reach into the maple center block. Between the two, really good acoustic coupling into the wood. Made quite a tone difference in a very good way. Had the bridge and the aluminum tail on for a while now, but the bushings really did the trick. The original bushings in the H535 are on the left, the ones on the right are Faber (aged nickel).
-
Yeah, my 2001 H535 fret issues are varied. I can set the truss rod to get the fretboard straight using a notched straight edge. However, at that setting, the frets are not leveled properly nor does the relief match the tops of the frets. Or set the truss rod to make the relief measured at the fret tops more correct, which makes the fretboard wonky. The other issue is the frets are rolled off too far from the treble edge, especially frets 1 - 5. I don't know if it was bad factory work or someone did a bad job on it before I owned it. 2001 was kind of a weird time at Heritage. Some real gems from that era, but seems like consistency was off. I did a bit of leveling and crowning and it is better. Not completely happy with it though. Planning on a full refret with Dunlop 6100, bit wider and a fair bit taller fret. That's what's on my H150 and it plays like butter. Going to do a full refret, lose the nibs, and pay attention to properly level the fretboard first before installing the new frets. Guitar sounds great, looks great, but I don't think it lives up to its potential without fretwork.
-
Yup, Gibson does it the same way and pretty much everyone else who winds up with nibs. Martin has been doing "pocketed" fret slots even on unbound fingerboards, so no visible fret tangs.
-
I think nibs are more of a process thing. Fretboards are mass produced and fretted before attaching to the neck. It's a lot easier to mass produce bound fretboards by installing the binding after the frets are installed, leveled, crowned and ends beveled. The board is shaped, with the channel for binding, then the frets installed and trimmed and dressed, then binding is glued on to the edge of the fretboard. Then it is trimmed level with eh edge of the wood, leaving a nib at the fret end. It's just faster and easier that way. I have a Martin acoustic with a bound fretboard (OMC-PA1 with ovangkal binding). Martin uses a "pocketed" technique to apply frets over the binding, with CNC doing all the precision work on the fretboard slots, leaving the bound part unslotted. (at least that's how it was explained to me at the Martin factory).
-
I took a real close look at both, my H150 (1998) and H535 (2001). I bought the H150 around 2001 at a guitar show, from Buffalo Brothers, who were a big Heritage Dealer long ago. They told me it was part of a special dealer run that they ordered in 1998. Their customer traded in for another guitar. Unlike most 1998 H150's, it came with a tune-o-matic bridge and tailpiece (nashville and heavy zinc, exactly like Gibson) and Seymour Duncan 59's. The H535 (2001) was a recent acquisition. It literally looks nearly unplayed, inside and out. It had the usual hardware on it, Schaller roller, top-loader tail, and HRW pickups. The hardware looks nearly factory new, as do the pickups. It looks like it was a case queen. I looked at the frets under magnification and measured them. I'm convinced they're factory, over the binding. They're also jumbo, larger than the H535. Looks like 57x110 (like Dunlop 6100). The binding is also different than my H535, much thinner. No nibs, as the board looks like it was bound, then fretted. Fretwork on the H150 is very high quality. Fretboard prep is really great on it, as well as the fret work itself. If it was a refret, I wanna meet that guy, cause it shows no sign of refret. Checking truss action with a notched straightedge (fretboard) vs. a ground straightedge (tops of frets) are pretty close to flat with each other. (sign of good board prep before fretting). By comparison, the H535 frets are almost certainly Jescar 47105 (.047x .104) wire. Nibs of course, binding is a lot deeper (front to back) than the H150. Fretboard and fretwork not as nicely done overall. There's really no wear on them, anywhere. Using the notched and ground straightedges, truss adjustment shows board flat vs. frets flat at very different settings. Means the fretboard prep wasn't as well done. While the fret tops are well dressed, the finished height from the top of the fretboard are significantly different all over the neck. It ranges from about .035 in the first few frets to about .044 above the 12th fret. Despite all that, the 535 still plays pretty well, sounds fantastic and looks beautiful. I'm considering perhaps refretting it the same as the H150. Would lose the nibs, but it would probably play very well.
-
A few weeks ago, I acquired a 2001 H535 with HRW's in natural maple. It's gorgeous and sounds great. The guitar seems to be nearly unplayed condition as well. Now that the excitement of newness has faded a bit, I note that the fretwork and the nut slotting were not the best work I've ever seen. This one has binding nibs over the end of the frets. By comparison, my 1998 H150 has fantastic fret work and plays like butter even after I've played the heck out of it for 20-something years. The nut is easy to adjust. The frets though, were shaped in a manner that lowers toward the fingerboard too far from the edge on the treble side. That and the nibs reduce the amount of 1st string playable area a bit. Had a few places with some poor leveling under the 1st string as well that were correctable. The fretwire appears to be the same as what was put on the H150, just leveled lower too far from the treble edge and with binding nibs. My H150 I've never had anything done to the frets, other than polish them from time to time. I've worn some divots in the lower frets, but not enough to warrant correction. I was under the impression that Heritage guitars didn't normally have the nibs in the late-90's-early-2000's, but I'm wrong about that? Kind of pondering a refret to get the H535 to play more like my H150 does. Lose the nibs in process, use the same wire on my H150 and same leveling process to maximize the playable area towards the edge of the fingerboard. Comments?